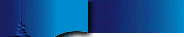
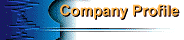
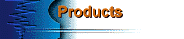

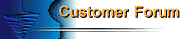
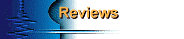
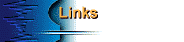
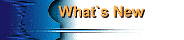
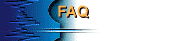
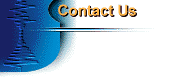
|

High-speed, high-efficiency inspection machines for detection, classification and documentation of flaws in electrical resistance welded pipe |
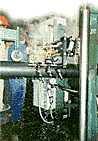 |
PRODUCT DESCRIPTION |
Introducing the AS-200e Series
The AS-200e Series 'Weld Inspector' is intended for high-speed ultrasonic inspection of longitudinal electrical resistance welded (ERW) pipe. The machine is installed for continuous on-line inspection, directly downstream from the welding head, or alternatively, is located off-line for the final inspection of cut pipe. Longitudinal ER welds in process or conveyor-fed pipe from 6" diameter are one-hundred percent inspected at pipe surface speeds to 1000mm/sec (20in/sec).
|
Mechanics
Inspection mechanics comprise a column or gantry-supported multi-channel, pneumatically loaded inspection head, with vertical adjustment for each pipe diameter. The basic inspection head accommodates two independently adjustable probe bubblers and wear shoes, for operation in a three-channel configuration. This provides inspection coverage of the weld from both sides of the seam, plus a confirmation of continuous ultrasonic coupling. Two additional probes, comprising three ultrasonic channels, are added for the inspection of thicker-walled pipes.
|
Probes
Type RSA angle beam probes are installed in AS-200e inspection machines. Suitable probe frequencies range from 2 to 5MHz, and are selected according to flaw sensitivity requirements for each pipe wall thickness to be inspected. Probes are aligned and fixed using water coupling bubblers and wear shoes with easy-to-use quick-disconnect fasteners.
|
Ultrasonic Hardware and Software
Inspection electronics comprise a usc-50.ultrasonic system computer, including a three channels in a dual-probe configuration and six channels for the four-probe configuration. Each channel is programmed with one to four signal gates and one or two alarm thresholds per gate. ScanMaster AS-200 production line software with the built-in AND/OR/NOR flaw classification utility provides for on-line flaw detection and evaluation.
|
AND/OR/NOR Flaw Classification
AND/OR/NOR inspection algorithms using gated ultrasonic signals from one or more channels are programmed for on-line 'event' classification. Up to twenty-two classifiers can be defined including two with hardwired digital outputs and twenty with real-time screen display.
|
Output Interface
A standard dual digital output interface is used for flaw marking by paint, with color codes to mark and differentiate flaws exceeding two different threshold levels. The digital interface can also be used for the operation of other devices, such as visual or audial alarm, and part sorters. An optional eight-channel digital output interface is installed for those applications requiring more than two flaw classification outputs.
|
Control Console
System operation is controlled from an operator console, comprising a 35U, environment-proof control cabinet, 17" color VGA monitor and keyboard, and usc-50 ultrasonic system computer. All machine functions, including ultrasonic instrument, I/O devices for paint marking, alarms and pneumatics, are accessed and controlled directly from the keyboard. During part set-up, the monitor provides a display of ultrasonic A-scan signals. During inspection, the monitor simultaneously displays the detection of 'events' for each channel along the part length plus a toggle-selected A-scan signal.
|
System Set-up Procedure
An ultrasonic parameter set-up file for each pipe diameter and wall thickness is stored on hard disk memory. The appropriate set-up file can be recalled manually by the operator, or, alternatively, is set automatically in response to an identification code downloaded by a host computer or bar code reader. Positioning of the probe bubblers is for each pipe diameter and wall thickness is set manually by the operator.
|
Remote Communication
The usc-50 system computer is equipped for direct communication with a host computer or remote data processing station, providing maximum flexibility for automation of inspection and data analysis procedures. Several communication protocols are offered for application-specific control reporting tasks. High-speed reporting of critical inspection results is useful for near real-time analysis of problems on the production line. Remote processing data is also especially effective in a facility where one or more inspection machines are installed.
|
Test Reports
A test report documenting inspection results is automatically produced at the end of each inspection sequence. Standard or tailor-made test reports are used. The report lists the detecting channel, gate and threshold level (1 or 2), position, strength (signal amplitude) and length along the weld line for each detected flaw.
|
SUMMERY INSPECTON SPECIFICATIONS |
Suitable pipe dimensions
From 150mm (6"in) in diameter and from 3mm (AAin) in wall thickness.
|
Inspection technique
Contact-type with probes fitted in holders, including hardened, replaceable wear shoes.
|
Number of inspection channels
Three to eight channels as per inspection specification. One to four programmable alarm gates per channel, with one or two operator-selected threshold levels per gate.
|
Transducers
Type RSA shear wave probes, 2, 2.25, 4 and 5MHz. Selection of 45, 60 and 70deg angle of propagation (in steel) for each channel. Elevated temperature (ET) option for on-line inspection.
|
Inspection coverage
100 percent of weld volume, dependent on number of probes and inspection frequency for each wall thickness and pipe diameter.
|
Inspection resolution
1mm (0.04mm) along weld line.
|
Flaw detection
Flaw detection to API Spec. 5L and 5CT, or as otherwise specified by the customer.
|
Inspection (feed) rates
Linear surface speeds to 1000mm/sec (40in/sec), dependent on external conveyor.
|
Safety Standards and Approvals
The AS-200e systems are fully compliant with the most stringent safety standards.
The AS-200e systems are CE certified for safety and electro-magnetic compliance.
|
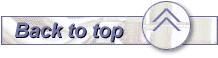
|